
Automatic Tool Change
CNC Spindles

EMG Precision's range of industrial grade, Automatic Tool Change (ATC), Ultra Precision, CNC Spindles with Water or Oil Cooling for CNC Milling machines and Routers. State-of-the-Art CNC Spindle Motors with featuring World-Class performance. Tool Sensor and Bearing Air Seal System as standard.
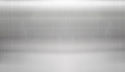


Automatic Tool Change
CNC Spindles explained...

explained...
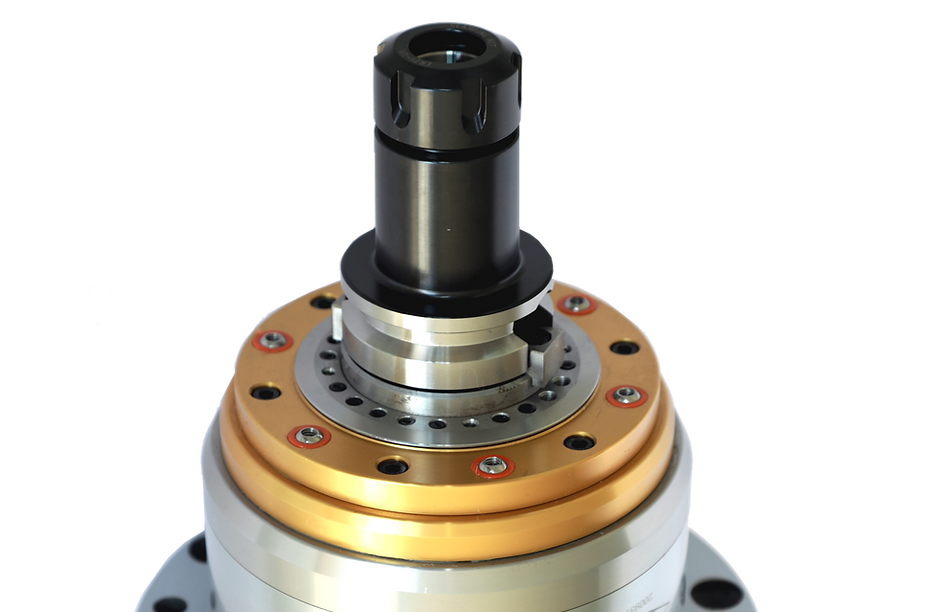


Automatic tool change, often referred to as an ATC, is used to improve both the production and the tool carrying capacity of a computerised numerical control or CNC machine tool. It does this by allowing the machine to work with various different tools. As such it is part of the process to achieve full automation.
BENEFITS of ATXC
-
ATC increases the machine tool’s productive time
-
It significantly reduces the times for changing worn tools.
-
It provides storage of the cutting tools, which are returned automatically to the machine tool after carrying out the required operations.
-
New cutting tools are automatically delivered to the machine by the tool-changing system.
-
Eliminate the time required to zero tools at each tool change.
MODERN | PRECISION | ENGINEERING | TAILORED
Automatic Tool Change CNC Spindle System
ATC Spindle BLOG Post EXTRACT...
The Automatic Tool Change Spindle system is a combination of various pieces of equipment that work together in order to enable continuous cnc machining. The system consists of a Tool Magazine, or sometimes called a tool rack, where a chosen number of tool types are stored, readily available to be automatically chosen and used.
This brings us to the Tool Changer System which is a device that is connected to your CNC control machine and performs the function of retrieving a tool from the Tool Magazine and delivering it to the ATC Spindle. Only Spindles with the ATC functionality can perform an interaction with the tool changer system...
Read the full article What is an Automatic Tool Change Spindle?
SHOP World-Class Precision Automatic Tool Change CNC Spindles
*FREE Worldwide Delivery is to applicable destinations that can be confirmed at checkout, but includes the majority if the United States, Europe, Canada & the UK.
The information provided by EMG Precision Ltd. (“we,” “us” or “our”) on www.emgprecision.com (the “Site”) and our mobile application is for general informational purposes only. All information on the Site and our mobile application is provided in good faith, however we make no representation or warranty of any kind, express or implied, regarding the accuracy, adequacy, validity, reliability, availability or completeness of any information on the Site or our mobile application.
MODERN | PRECISION | ENGINEERING | TAILORED
All ABOUT CNC Spindles
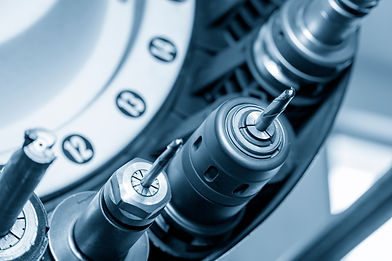
Author: Jonathan Gee 28 March 2021
What is an Automatic Tool Change Spindle?
Introduction to Automatic Tool Change Spindle Motors
It is almost unimaginable to envision all the possible types of CNC machining centres that could be conceived but regardless of whether you install an ATC spindle on a basic 3 Axis router, or a bespoke, behemoth of a machine as big as a house, the fundamental principle of an Automatic Tool Change system remains the same.
Here we are going to talk about many systems and processes that at first sound unrelated, when in reality are all, and only made possible with the use of an Automatic Tool Change Spindle. Most of these functions can be performed with Manual Tool Change Spindles, but the time required and subsequent costs can make it very impractical. In order to fully take advantage of the potential benefits of a fully computer numerically controlled machining system, an ATC Spindle is an essential component in any streamlined, efficient machining shop.
Lets be clear when we say that Automatic Tool Change Spindles are not only for those with deep pockets or the biggest professional industries, but also for the avid DIY’er or ambitious beginner alike. ATC Spindles are also not only unused for machining a variety of metals, but business and individuals all over the world use ATC spindles for machining plastics, woods, composites and many other materials as well as machining aluminium, stainless steel, cast irons and other metals.
An efficiently set up and working Automatic Tool Change Spindle can open up a whole world of opportunities for your CNC machine, and when coupled with a precision Tool Height Setter and Wireless CNC Touch Probe, the avenues for optimising automation is really endless. Lets dig into what it’s all about in a little more depth step-by-step.
Performing CNC Tool Changes
Pick the tool to fit the job is a very relative saying when it comes to automatic tool changers. Often, machined parts require a various number of different tools in order to complete the job. It is not always absolutely necessary to have multiple types of tool to complete machining a particular project, but more often than not it is required to provide the efficiency needed to remain competitive. Consider a situation whereby you perform roughing functions with a large tool diameter and them more finer detail, with finishing tools and passes. A certain number of tool changes are required to complete the task, and the more tool changes, the more time is lost attributed to down time. Not only does the changeover time include untightening, removing and clamping in a new tool, but the CNC system needs to re-measure the physical length of the tool in order to know where the machine is cutting.
Manual and Automatic Tool Change Systems
In a manual tool change system, it is necessary to measure the height of the tool after each tool change and enter that measurement into a cnc system. The combination of all this downtime can increase the cycle time of a component dramatically and make the part financially unprofitable. An automatic tool change system does not remove the need for future tool changes, but what it does do is automate the process and remove some tasks that are normally mandatory with manual tool changes.
ATC System Overview
The Automatic Tool Change Spindle system is a combination of various pieces of equipment that work together in order to enable continuous cnc machining. The system consists of a Tool Magazine, or sometimes called a tool rack, where a chosen number of tool types are stored, readily available to be automatically chosen and used. This brings us to the Tool Changer System which is a device that is connected to your CNC control machine and performs the function of retrieving a tool from the Tool Magazine and delivering it to the ATC Spindle. Only Spindles with the ATC functionality can perform an interaction with the tool changer system.
Tool Height Setting Calibration
Now it is necessary to calibrate the height of the newly installed tool with the use of a Tool Height Setter, or sometimes called a CNC Touch Plate. This device measures the height of the installed tool by running a program that lowers the tool on the tool plate until it touches, essentially measuring how long the tool is in the spindle tool holder. Here is where a large efficiency saving can be made with and ATC Spindle, over more traditional Manual Tool Change Spindles. With most CNC systems it is possible to store the information for various tools in the Tool Magazine, in what’s usually called a Tool Table.
WORLD-CLASS ULTRA PRECISION CNC MACHINING SPINDLES
Tool Table
In this Tool Table all the measurements for tool heights can be stored so the Tool Height Setting process does not have to be performed at every tool change. More often than not though, due to this process now being automated and much quicker than if it were performed manually, the Tool Height Setting measurement is taken with each tool change to perform additional functions. With an ATC system, it is also possible to perform, tool wear measurements, automatic broken tool detection and you can even store a wireless cnc touch probe in the Tool Magazine, in order to automatically perform probing functions.
How does an Automatic Tool Change Spindle Motor work then?
We won’t delve into the CAM program too much but at some point during the machining operations it may be necessary to perform an automatic tool change. At this point the machine receives a tool change command which immediately prompts the spindle to stop rotating, and to move to a pre-programmed location relative to the Tool Changer System and/or Tool Magazine/Rack.
Depending on the design of the system, there may be an articulating arm or indexing conveyor of some description that delivers the tool holder from the magazine to the ATC spindle and vice versa. Alternatively the Tool holder maybe delivered back and forth from the Tool Magazine directly by the ATC Spindle. The programmed CAM and Tool table will dictate which tool position in the Tool magazine is required and the CNC system will automatically retrieve the required tool and install it in the ATC Spindle. When a tool is already installed in the spindle, the system will deliver the no longer required tool to an empty location in the tool carousel, and then proceed to retrieve the next required tool in order to proceed with the next machining operation.
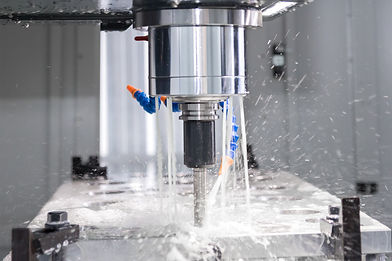
MODERN | PRECISION | ENGINEERING | TAILORED

In the most efficient Tool Change systems, the removal of the old tool and the selection and delivery of the new tool are completed in one operation at the same time in order to reduce the changeover time to as little as possible.
At this point, a variety of functions can be automatically performed including, but not limited to, automatic Tool Height Setting, Touch Probing, Cutter Compensation, Broken Tool Detection.
ATC Compatible Tool Holders
There are a variety of types of Tool Holder that are designed to function with automatic tool change systems, each of which have a slightly different form or method of clamping into the Spindle itself. This is a huge topic in itself and warrants its own feature topic. Some popular choices of ATC compatible Tool Holders are MAS403 BT Tool Holders, DIN69893 HSK Tool Holders, ISO, CAT, NT and more.